Prototype Construction
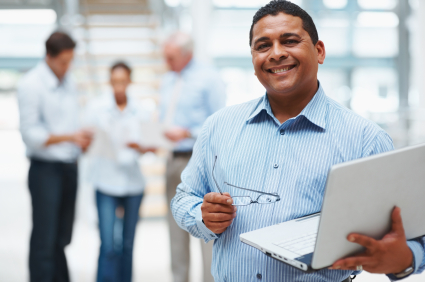
There are several options for translating a virtual or non-functional prototype into a functional product prototype. The prototyping method a company chooses for their product will depend on the audience, purpose and budget. Best results are achieved by a complementary partnership between the product’s parent company and a team of outside experts. The knowledge of an expert team will supplement your company’s goals with the skill and experience needed to complete the project in a timely and affordable manor.
Ideally a series of virtually engineered designs, on CAD or other software, will precede the functional prototyping process. In cases where an previous prototype exists and there are no digital data for the design it is possible to scan the item and repair the design. In this scenario it is important to consult an expert to see what the best solution is.
This is a comprehensive list of functional prototype creation methods:
Selective Laser Sintering
These prototypes are made of strong, durable polyamide material that allows for a broad range of functional testing.
Typical Uses: Snap fits; working hinges; lighting elements, ventilation systems, high thermal loads (with glass filling); and many others
Vacuum Casting
These prototypes are ideally used for functional plastic prototypes, in quantities less than 20.
With a vast selection of materials to choose from, including various polyurethanes, allow these prototypes to be used for functional testing in various conditions.
Tooling in Aluminum Molds
Aluminum tooling is great for rapid and cost effective production of quality components. Other mold tools can take a minimum of 3 months to deliver; subsequently traditional injection molding can be extremely expensive and time consuming. With the speed and reasonable costs of aluminum molds designers can experiment and produce more products inventive. By using aluminum mold tools it is easy to create a fully functional prototype in the materials for manufacture without excessive cost. Due to current Aluminum grades and strength, this type of mold can produce between 100,000 and 1,000,000.
RIM (Reaction Injection Molding)
This method produces premium quality plastic parts with a short lead-time. RIM is ideal for large components in quantities of 10 to 2000. The process uses low pressure injection technology. RIM molding is used often in the car industry because of its quality and speed.