3D Printed Rocket Engine Parts Pass Hot Fire Test
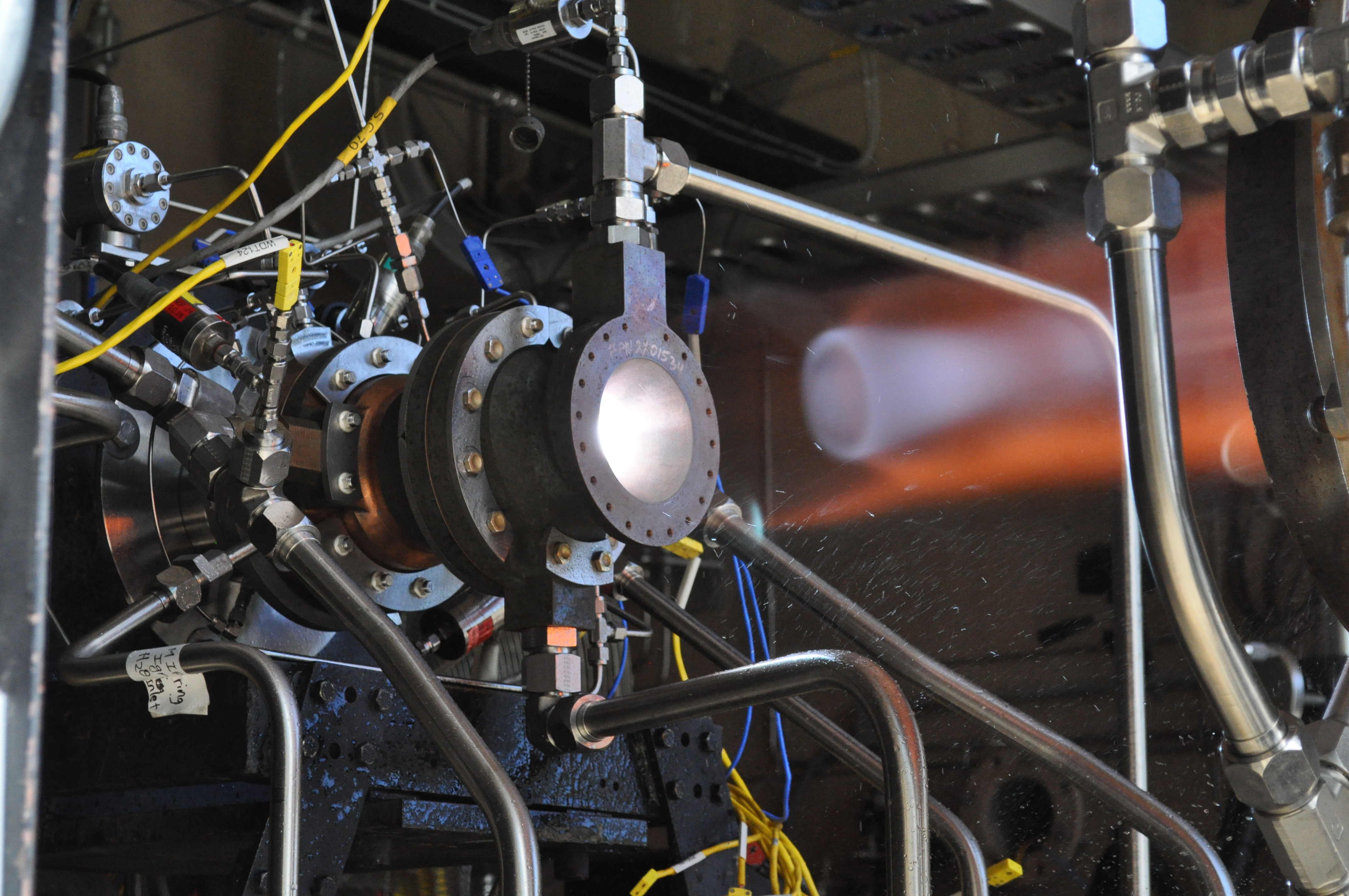
The technology of additive manufacturing, more commonly known as 3D printing, is dramatically influencing the way companies design and build machinery for a wide variety of applications.
NASA has recently become interested in additive manufacturing as a way to cheaply and expeditiously run necessary tests. In partnership with Aerojet Rocketdyne, NASA recently completed the first hot-fire tests on a copper-alloy rocket engine thrust chamber assembly, marking the first time that rigorous tests proved that parts manufactured by a 3D printer can withstand the severe stresses inflicted upon combustion engines in an actual space launch. NASA and Aerojet Rocketdyne conducted 19 tests in all. The test subjects were four injector and thrust assembly configurations. NASA explored various injector operability points and fuel mixture ratios. All of the tests were determined to have terminated successfully.Tyler Hickman, lead engineer for the testing performed at NASA’s Glenn Research Center, was elated with the results. “The successful hot fire test of subscale engine components provides confidence in the additive manufacturing process and paves the way for full scale development,” he said.
NASA’s groundbreaking tests have wowed many scientists and proponents of additive manufacturing. As Aerojet Rocketdyne put it, copper alloy presents a complex challenge during the 3D printing process. As the copper’s elements are brought down to a micro-scale, the material’s properties are often significantly sub-standard when compared to typical copper. Aerojet Rocketdyne found a way to discover and exploit processing characteristics. The company performed rigorous testing on the copper alloy in order to determine how the alloy performs in the environment of a 3D printer.
According to Paul Senick, project manager at Glenn Research Center, “Additively manufactured metal propulsion components are truly a paradigm shift for the aerospace industry. NASA and its commercial partners continue to invest in additive manufacturing technologies, which will improve efficiency and bring down the cost of space launches and other earth applications.”